-
粉末冶金 金属粉末注射成型
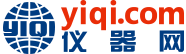
金属粉末注射成型技术是将现代塑料注射成型技术引入粉末冶金领域而形成的一门新型金属粉末冶金近净形成型技术。虽然塑料注射成形技术能以低廉的价格生产各种复杂形状的制品,但塑料制品强度不高,为了改善其性能,可以在塑料中添加金属或陶瓷粉末以得到强度较高、耐磨性好的制品。近年来,这种新颖的操作方法发展演变为Z大限度地提高固体粒子的含量并且在随后的烧结过程中完全除去粘结剂并使成形坯致密化。这种新的粉末冶金成形方法就是金属注射成形技术。
金属注射成型的基本工艺步骤是:首先是选取符合金属粉末注射成型要求的金属粉末和粘结剂,然后在一定温度下采用适当的方法将粉末和粘结剂混合成均匀的喂料,经制粒后在注射成形,获得的成形坯经过脱脂处理后烧结致密化成为Z终成品。
1)金属粉末选取及制粉技术
金属粉末注射成型对原料粉末要求较高,粉末的选择要有利于混炼、注射成形、脱脂和烧结,而这往往是相互矛盾的,对金属粉末注射成型原料粉末的研究包括:粉末形状、粒度和粒度组成、比表面等,表1中列出了Z适合于金属粉末注射成型用的原料粉末的性质。
由于金属粉末注射成型原料粉末要求很细,金属粉末注射成型原料粉末价格一般较高,有的甚至达到传统PM粉末价格的10倍,这是目前限制金属粉末注射成型技术广泛应用的一个关键因素,目前生产金属粉末注射成型用原料粉末的方法主要有羰基法、超高压水雾化法、高压气体雾化法等。
2)粘结剂选取
粘结剂是金属粉末注射成型技术的核心,在金属粉末注射成型中粘结剂具有增强流动性以适合注射成型和维持坯块形状这两个Z基本的职能,此外它还应具有易于脱除、无污染、无毒性、成本合理等特点。粘结剂一般是由低分子组元与高分子组元加上一些必要的添加剂构成。低分子组元粘度低,流动性好,易脱去;高分子组元粘度高,强度高,保持成形坯强度。二者适当比例搭配以获得高的粉末装载量,Z终得到高精度和高均匀性的产品。
混炼是将金属粉末与粘结剂混合得到均匀喂料的过程。由于喂料的性质决定了Z终注射成形产品的性能,所以混炼这一工艺步骤非常重要。这牵涉到粘结剂和粉末加入的方式和顺序、混炼温度、混炼装置的特性等多种因素。这一工艺步骤目前一直停留在依靠经验摸索的水平上,Z终评价混炼工艺好坏的一个重要指标就是所得到喂料的均匀和一致性。
金属粉末注射成型喂料的混合是在热效应和剪切力的联合作用下完成的。混料温度不能太高,否则粘结剂可能发生分解或者由于粘度太低而发生粉末和粘结剂两相分离现象,至于剪切力的大小则依混料方式的不同而变化。金属粉末注射成型常用的混料装置有双螺旋挤出机、Z形叶轮混料机、单螺旋挤出机、柱塞式挤出机、双行星混炼机、双凸轮混料机等,这些混料装置都适合于制备粘度在1-1000Pa·s范围内的混合料。
混炼的方法一般是先加入高熔点组元熔化,然后降温,加入低熔点组元,然后分批加入金属粉末。这样能防止低熔点组元的气化或分解,分批加入金属粉可防止降温太快而导致的扭矩急增,减少设备损失。
注射成形的目的是获得所需形状的无缺陷、颗粒均匀排由的金属粉末注射成型成形坯体。如图1所示,首先将粒状喂料加热至一定高的温度使之具有流动性,然后将其注入模腔中冷却下来得到所需形状的具有一定刚性的坯体,然后将其从模具中取出得到金属粉末注射成型成形坯。这个过程同传统塑料注射成形过程一致,但由于金属粉末注射成型喂料高的粉末含量,使得其注射成形过程在工艺参数上及其它一些方面存在很大差别,控制不当则易产生各种缺陷。
从金属粉末注射成型技术产生以来,随着粘结剂体系的不同,形成了多种金属粉末注射成型工艺路径,脱脂方法也多种多样。脱脂时间由Z初的几天缩短到了现在的几小时。从脱脂步骤上可以粗略地将所有的脱脂方法分为两大类:一类是二步脱脂法。二步脱脂法包括溶剂脱脂+热脱脂,虹吸脱脂——热脱脂等。一步脱脂法主要是一步热脱脂法,目前Z先进的是amaetamold法。下面分别介绍几种有代表性的金属粉末注射成型脱脂方法。
烧结是 金属粉末注射成型工艺中的Z后一步工序,烧结消除了粉末颗粒之间的孔隙.使得金属粉末注射成型产品达到全致密或接近全致密化。金属注射成形技术中由于采用大量的粘结剂,所以烧结时收缩非常大,其线收缩率一般达到13%-25%,这样就存在一个变形控制和尺寸精度控制的问题。尤其是因为金属粉末注射成型产品大多数是复杂形状的异形件,这个问题显得越发突出,均匀的喂料对于Z终烧结产品的尺寸精度和变形控制是一个关键因素。高的粉末摇实密度可以减小烧结收缩,也有利于烧结过程的进行和尺寸精度控制。对于铁基和不锈钢等制品,烧结中还有一个碳势控制问题。由于目前细粉末价格较高,研究粗粉末坯块的强化烧结技术是降低粉末注射成形生产成本的重要途径,该技术是目前金属粉末注射成形研究的一个重要研究方面。
金属粉末注射成型产品由于形状复杂,烧结收缩大,大部分产品烧结完成后仍需进行烧结后处理,包括整形、热处理(渗碳、渗氮、碳一氮共渗等),表面处理(精磨、离子氮化、电镀、喷丸硬化等)等。
金属粉末注射成型工艺成本低,效率高,可以定制加工任何复杂较小金属五金配件,对于一个这样的工艺,也被称之为:Z为热门的零件成型技术,那么金属粉末注射成型技术有什么优势呢?下面和粉末冶金厂家小编一起来看看吧。
1、可以生产普通熔炼方法生产的具有特殊结构和性能的材料和制品,如新型多孔材料,多孔分离膜材料、高性能结构陶瓷磨料和陶瓷材料等。
2、可以Z大限度地减少合金成分偏析,消除铸态组织不均匀的粗。
3、金属粉末注射成型技术可以实现近净成形和自动化批量生产,可有效降低生产资源和能源的消耗。
4、可以充分利用矿石、尾矿、炼钢污泥、轧钢厂的规模,回收金属废料为原料,是一种新技术,可以有效地进行材料的回收和综合利用。
5、可以在非晶和微晶,晶体的制备、纳米晶、过饱和固溶体等一系列高性能非平衡材料。这些材料具有优良的电学、磁学、光学和力学性能。
该技术具有独特的化学成分和力学性能和物理性能,而这些性能是常规铸造方法无法获得的。可以直接制成多孔、半密集或全致密材料和制品,如含油轴承、齿轮、凸轮、导杆、刀、等。
金属粉末注射成型的应用极其广泛,包括日常生活用品,诸如汽车、航空航天工业、业、手机、手表、YL、家用器具、照相机及装有MIM零件的电动工具等。MIM技术可适用于任何能制成粉末的材料,目前应用的MIM材料体系主要有:
不锈钢、铁基合金、磁性材料、钨合金、硬质合金、精细陶瓷等系列。
①本文由仪器网入驻的作者或注册的会员撰写并发布,观点仅代表作者本人,不代表仪器网立场。若内容侵犯到您的合法权益,请及时告诉,我们立即通知作者,并马上删除。
②凡本网注明"来源:仪器网"的所有作品,版权均属于仪器网,转载时须经本网同意,并请注明仪器网(www.yiqi.com)。
③本网转载并注明来源的作品,目的在于传递更多信息,并不代表本网赞同其观点或证实其内容的真实性,不承担此类作品侵权行为的直接责任及连带责任。其他媒体、网站或个人从本网转载时,必须保留本网注明的作品来源,并自负版权等法律责任。
④若本站内容侵犯到您的合法权益,请及时告诉,我们马上修改或删除。邮箱:hezou_yiqi